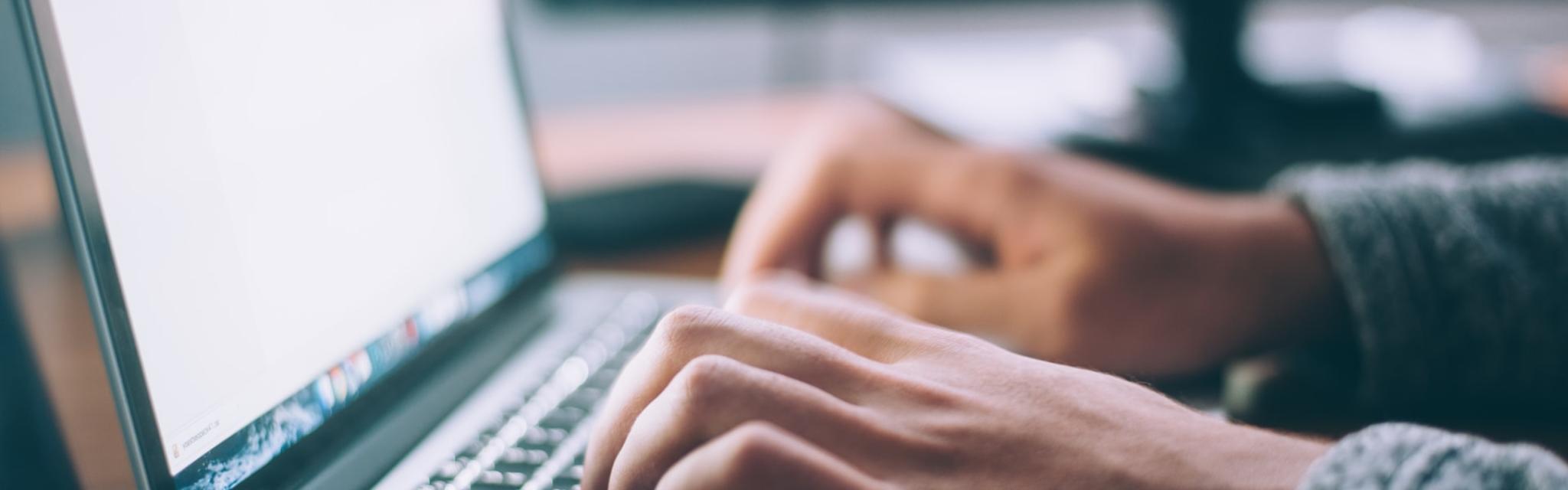
Cold forging is a metal-shaping process performed at an ambient temperature, which should be 30% below the metal’s recrystallization temperature. The metal workpiece, usually a slug or a blank is inserted into a die and shaped through pressing, squeezing or drop forging hammers. By deforming the metal in fast succession, very complex shapes can be achieved. Cold forging has a great impact on the mechanical properties of the metal as structural integrity, fracture toughness and fatigue life.
Why is cold forging a critical manufacturing process?
During cold forging, the metal is forced to flow into the desired shape by filling the die. This requires sufficient flow properties, otherwise the shaping process will result in cracks. Some deformation techniques may also make the metal buckle, provoking folds. All this can be avoided with the proper types and sequence of operations. For instance, laps can be avoided if the workpiece is upset prior placing it into the die.
The tool design and manufacture are also of critical importance. When improperly treated, the dies can easily get damaged because of overloading, low cycle fatigue or abrasive wear.
Which industries mostly benefit from cold forging?
Cold Forged Shafts
Every industry that requires strong components with close tolerances, manufactured in high-volume runs, can take advantage of cold forging. Some of the most common cold forged parts include, among others:
- Shafts
- Hollow shafts
- Nail
- Screws
- Rivets
- Fasteners
Cold Forging Techniques
A complete cold forging process comprises a sequence of several cold forming techniques to produce the final shape. The three main techniques are: forward extrusion, reverse extrusion and upset. The last one is also known as cold heading, because it is mainly used to form “heads” of fasteners. Depending on the complexity of the desired shape, the following processes or a combination of them may be needed:
- bending
- coining
- ironing
- punching
- piercing
- squaring
- blanking
- threading
- trimming
Every single manufacturing step of the cost effective cold forging process can be automated.
Cold Forging Equipment
Cold forging can be performed on vertical mechanical or hydraulic presses (with one or more stations), or on a cold-forming machine. The pre-heated workpiece is transferred from one station to the next at a very high speed and every section performs a specific operation. For instance, a cold-forming machine can be a single die, two-blow process one; a two die, three-blow process one or a multiple-die forming one.
This production cycle suits very well big volumes. Moreover, the geometry of the shapes can vary from the easiest to the most complex components, with thin and long sections, incorporating all kind of design elements as webs, flanges or protrusions.
Cold Forging Benefits
Better Surface Finish
A high-quality cold forging sequence can easily eliminate the need for post-forging treatments such as welding or machining. This enables the manufacturing of near net shape components.
Enhanced Mechanical Properties
Due to improved dimensional stability, cold forged metal doesn’t perform any structural changes and keeps all its original mechanical and tensile characteristics. Those can be even enhanced, resulting in improved grain structure.
Reduced Production Cost
Cold forging doesn’t require expensive heating equipment and tooling for costly secondary operations. Compared to machining, 70% more used material can be saved. And last, but not least – this is a high-speed manufacturing process, which can deliver up to 450 pieces per minute.
Cold forging is a highly cost effective manufacturing process, enablling to produce components with improved strength.
Farinia Group, through Setforge, offers high-quality cold forging process, consisting of the best sequence of techniques adapted to the part’s shape and size. Our equipment includes state-of-the-art presses and lines operated by experienced engineers and workforce. We are one of the main European suppliers of cold forged shafts for the automotive industry.