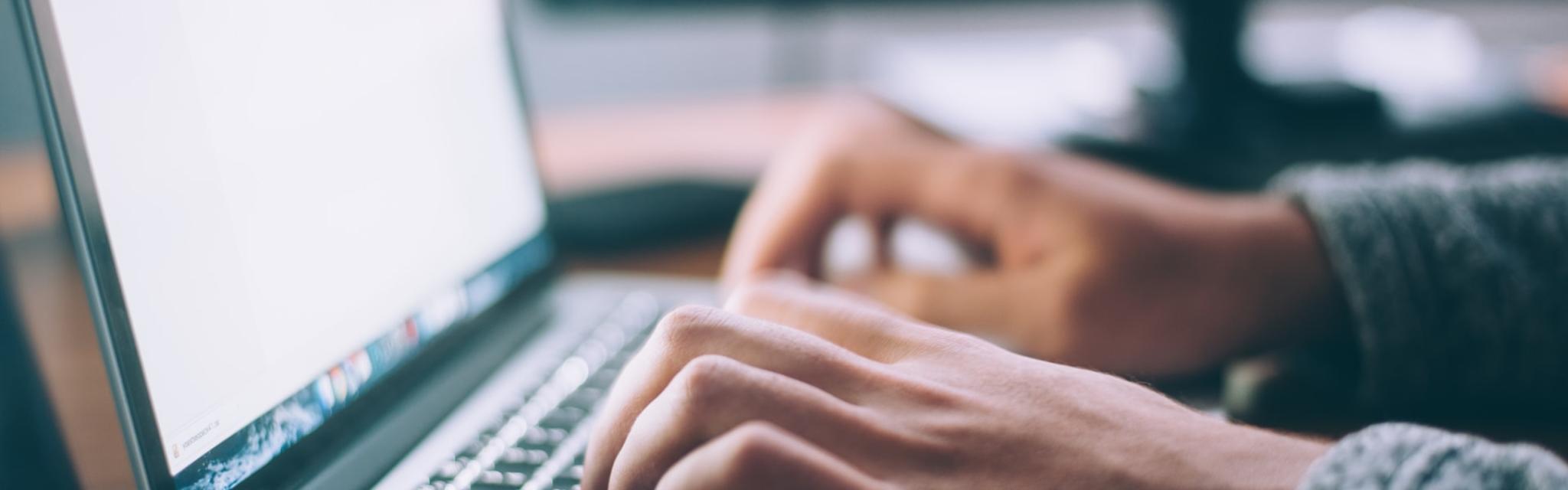
Mankind’s ecological footprint far exceeds Earth’s long-term capacity, according to the climate scientists. Energy generation and industrial activities are often pointed out as major emitters of greenhouse gases, the "anthropic" contributors to the global warming.
Insofar as ecological considerations have a rising importance and environmental legislations become prominent, sustainable development starts with eco-friendly manufacturing. Eco-manufacturing is a pillar of sustainability development and any reduction in the huge amounts of energy and materials consumed can help limiting the global warming.
Powder-bed metal additive layer manufacturing processes (DMLS, EBM) are gaining an increasing interest from industry, as the quality of AM parts improves. They enable to realize complex geometries (inner shapes, lattice structuring) and functionally improved components (lighter, ergonomics) or to consolidate large systems into fewer components. Technology has made significant strides in metallic ALM materials and processes and 3D printed parts now exhibit similar or sometimes superior mechanical properties than their conventional counterparts.
One of the major mainstays of AM development in the next years is its apparent environmental friendliness through low material wastes, no tooling and the possibility to produce different parts at a time. Design for Additive Manufacturing leverages the unique design freedom and allows superior functional integration and part consolidation. It can spar significant resources/energy consumptions (and pollutant emissions) in upstream and during manufacturing, assembly and at the end of the lifecycle, during the disassembly of products.
Let’s try to set a mindful and objective evaluation of metal ALM sustainability potential.
How to quantify sustainability and environmental impacts?
Any sustainable decision-making process must conciliate the environment and socio-economic aspects.
Environment is one of the key components of a global sustainability approach.
Social impacts (occupational safety and health, employment consequences) are not well known because ALM is still paving its way to the society and industrial world.
From the environmental standpoint, a life cycle assessment (LCA) is a systematic approach that reduces the chance of transferring impacts from a stage of the product's lifecycle to another and helps to capture the true benefits and possible pitfalls of ALM. The LCA methodology quantifies, from “cradle-to-grave”, every elementary stages of a product’s life cycle, in terms of in-flows and out-flows of materials and energy (consumptions of resources/energy and emissions in air, soil and water, land occupation).
LCA is an iterative and systematic, “cradle-to-grave” process that evaluates the environmental impacts of products, processes, and services. Its quality depends on the life-cycle inventory data it uses.
What are the elementary stages of a metal ALM product?
As young processes presently on the hype, the environmental ins and outs of components issued from ALM are not well known due to the lack of investigation. However, the usual lifecycle can be described as composed of some elementary stages, each qualified by a few relevant questions, which help finding out the contribution of each stage in respect with the total environmental impacts.
The list of questions is not exhaustive but shows well how versatile is the environmental profile. An understanding of the functional goals behind the design helps to minimize environmental impacts through the whole supply-chain configuration and avoid simply moving consumptions/pollutions from a stage to another without global benefits.
What impacts the environmental performance at each stage of the life-cycle?
Material extraction and powder preparation
Production of metal powders commonly involves melting raw material, atomizing them and solidifying the resulting metallic powders : This is what processes based on "atomization" usually do. Another technique is the solid-state reduction, where a selected ore is crushed, typically mixed with carbon, and passed through a continuous furnace. In the furnace, a reaction takes place, reducing the carbon and oxygen from the powder, that leaves a cake of sponge metal which is then crushed, separated from all non-metallic material, and sieved to produce powder.
Oxide reduction and water atomization are limited with respect to special powder quality criteria, such as particle geometry, morphology and chemical purity. High-grade metal powders for ALM require characteristics that are not typically found in atomized powders for press and sinter applications. Therefore, inert gas atomization combined with melting under vacuum is the leading powder-making process.
While usual material elaboration processes are well reported in LCI-databases, atomization processes are still poorly documented. To fairly compare ALM and traditional processes, consumptions and emissions have to be investigated, from the sourcing and transportation of the raw melted material to the process itself (Argon, overall wastes).
Erasteel presents its atomization process of metal powders with a clear and understandable animation.
Manufacturing (powder-bed metal ALM)
Traditionally, every product follows a particular manufacturing path and requires tooling. The volume of material machined away depends on the final geometry and the preformed raw material (sheet, rods or block). Very few methods exist to quantify precisely environmental impacts of traditional manufacturing processes. It is often left aside, neglected or subject to estimation (which makes sense in the scope of traditional large serial volumes, where impacts are amortized over a large number of items).
An advantage of ALM that has received little attention is the unprecedented level of transparency with respect to the energy and material inputs that the (quasi) single-step nature of ALM process offers, even though post-build operations are often performed to ensure customers' specifications.
Elementary powder-bed ALM’s modes are preheating the chamber, creating the inert atmosphere, energy source exposure, recoating a new layer, final cooling down and part/powder extraction (cleaning) while the flows of interest are materials (powders, wastes), fluids (nitrogen, argon) and electrical consumption (of each feature of the machine).
In a process-based LCA, inputs (materials and energy resources) and outputs (emissions and wastes to the environment) are itemized for a given step in producing a product. During manufacturing of metal ALM products, items are as in the image above.
Electric consumption
Conventional milling machines, heavy presses and melting machines are globally more energy intensive in total than ALM systems. For the same production versatility, ALM requires a single machine using a laser beam. This difference in large unit production can be critical for the total energy consumption and the environmental footprint of an industrial line.
Conversion with an impact assessment method (Eco-Indicator 95) offers a single unit of measurement (mmPts) to cumulate all different sources of environmental impacts (materials, fluids and electrical consumption).
As ALM lasers’ energy efficiency typically ranges 30-50%, machines embed an energy-consuming laser cooling unit which is active during all modes of the production. In addition, the process heaters (chamber, frame and platform) also consume a large amount of energy, enforcing the relevance of a proper insulation.
The building time and thus energy consumption can be reduced by minimizing the building height of the batch, for example by optimizing the nesting efficiency or the part orientation. For this reason, the part shape and manufacturing parameters are crucial.
Capacity utilization
Due to the parallel characteristics of additive processes, the capacity utilization rates impacts the total energy inputs. Full capacity utilization results in lower specific energy consumption but the saving varies heavily from a platform to another and it is critical for the energy efficient operation of some ALM systems.
Contributing factors to the large variations are the extensive energy expenses in atmosphere generation, warm-up and cool-down (DMLS, and particularly EBM). Operating those machines at full capacity will result in far greater energy efficiency (the energy consumption is allocated to a far greater part mass), thereby reducing the specific energy consumption compared to a low capacity production, which severely penalizes environmental performance.
Generation of wastes
Subtractive manufacturing methods produce useless chips (that should be recycled), which are eventually a drag on the environment. ALM has a better environmental standing as it only uses the material that is needed. Although in metal powder-bed systems, wastes are generated in terms of support material and used powder, the processes are highly material efficient in terms of reusability.
Distribution of printed parts
ALM lowers the cost for entry into manufacturing into a given location. Indeed, a single machine can handle a high variety of designs, as well as print different parts at the same time. ALM is therefore particularly suited to distributed manufacturing which allows to set the production location at the optimum distance between the material resource and the customers. As a consequence, less packaging and transportation are required which reduces energy consumption and air emissions during the distribution.
Utilization
ALM’s ability for complex design can bring major gains during use life. Product geometry can be optimized for a lighter weight or improved functionality. Either way it can reduce the energy and natural resources consumption during the application they were designed for, a positive impact on the environment.
For aerospace components and those used in mobility applications, a shift from traditional techniques to ALM is rewarded during the utilization stage of the life-cycle, the most impacting regarding the environmental performance. 1 kilogram removed from every aircraft of a 600+ fleet of commercial jet-liners saves every year about 90’000 liters of fuel and avoids the emission of 230 tons of CO2 in the atmosphere.
Outlook
Regarding efficient operation of machines, environmental impacts per manufactured part depend more on machine utilization than on its type or size. From a sustainability standpoint, maximizing utilization by sharing machines is of top-priority for all ALM machines.
The proper choice of the equipment (optimal size process chamber) allows producing a wide variety of products (batches) on the same machine, limiting the environmental impact.
ALM reduces the material waste stream, relevant for high-end materials. However, it is not intended to replace traditional subtractive manufacturing, but offers an eco-friendly alternative to reduce the environmental impacts (light-weighting) in applications where utilization stage of life-cycle is intensive in terms of energy and CO2 (mobility).
Regarding machines, more eco-friendly metal powders must be developed, renewable energy widely adopted, and heat flows and process energy management be improved.
Life-cycle databases for LCA modeling software must be developed in order to facilitate and speed up the environmental analysis of ALM.
Spartacus3D understands that metal ALM is at a tipping point, about to go mainstream in the industry. The technology has moved well beyond prototyping and tooling to create durable and safe products. We aim to understand every aspect of the technology to offer our customers the most sustainable and adapted solutions.