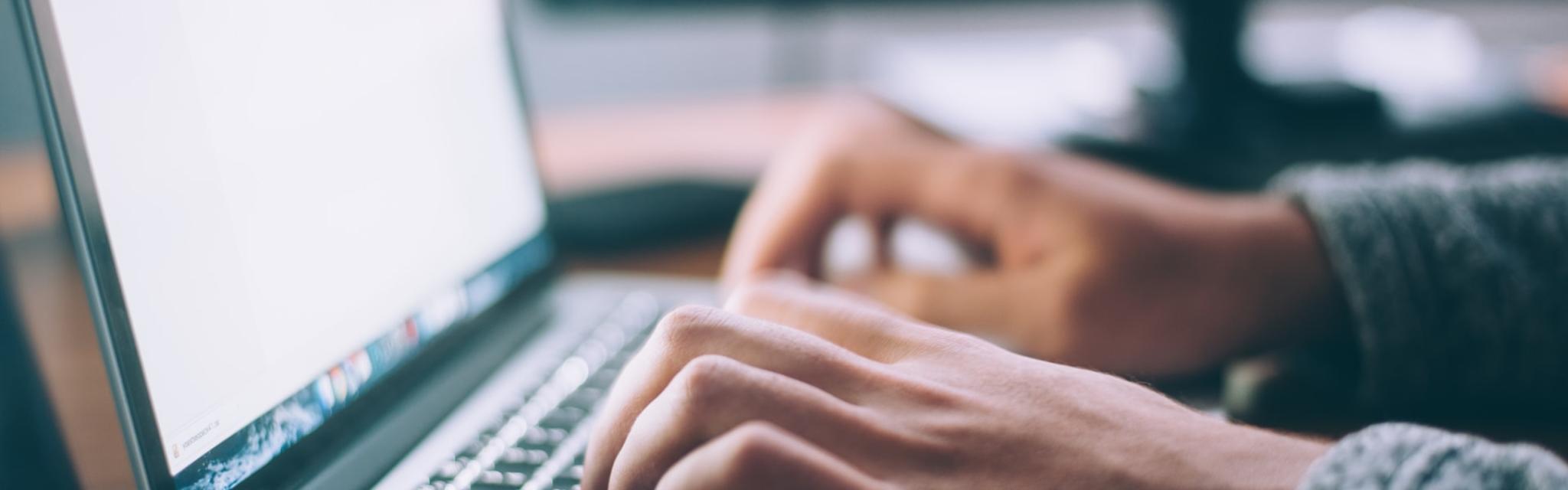
Metal additive manufacturing is becoming an economically viable choice to manufacture complex serial parts in small batch sizes. An increasing number of companies are using additive manufacturing (AM) over conventional processes (machining, forging and even casting) to produce high-end products with a competitive advantage.
Advantages of additive manufacturing for industries with high-value/low volume components such as aerospace and defense or medical implants have been praise enthusiastically and publicly for some years already.
The unequalled design freedom in AM is typically leveraged through:
- Part consolidation
- Weight reduction
- Functional integration / customizationh
- Superior aesthetics
- Manufacturing footprint reduction
Additive Manufacturing and “Complexity for Free”
A promising ability offered by AM is design freedom combined with methods for optimization.
Design freedom pushes complexity to new limits:
- Shape complexity: AM virtually enables any shape. The benefits of shape optimization can be exploited in customized and complex geometries.
- Hierarchical complexity: Multi-scale structures can be designed and built from the microstructure through the mesostructure (scale sizes in the millimeter range) to the macrostructure scale of a part.
- Material complexity: Material can be processed specifically at one point or layer at a time. It enables the creation of parts with complex and varying material compositions and thus, material property gradients.
- Functional complexity: Fully functional assemblies and mechanisms can be fabricated right away.
The potential of AM radically changes product design and the usual development process. The possibility of integrating additional features to improve product performance at the same costs challenges the traditional manufacturing paradigm that struggles to conciliate geometric complexity and performance with low unit cost.
AM offers an unrivalled level of complexity, often denoted as “complexity for free” when compared with what traditional methods of manufacturing can achieve.
As a consequence, AM encourages “Design for Manufacture and Assembly” to evolve into “Design for Function”, where the only limitation is the imagination of the designer and its ability to implement appropriate design principles.
Overpass the Traditional Scope to Fully Embrace New Capabilities
Nowadays, engineers widely use the principles of Design for Manufacturing and Assembly (or DFMA) for parts and assemblies. They apprehend the classic design methodology where, for example, mold-based production techniques are at the forefront. Designs are tailored with more homogeneity to reduce the cost of the mold, and thus, the cost of the final product. Such designs use to compromise functional performance for a cheaper if not merely feasible manufacturing or assembly (and reduced logistic costs).
In traditional engineering design, DFMA principles rely partly on the limitations of traditional manufacturing methods and machining tools. Moreover, common type of billets (metal sheets, beams, rods and shafts) and their shape strongly influence the definition of designs, leading engineers towards simple geometrical shapes.
Accordingly, CAD environments drive engineers to the wide adoption of straight lines and right angles (90 degrees) in their blueprints. While straight lines are obviously the most common geometrical entities, another one with a strong tradition is the circle which is mostly used when engineers design holes or bearing seats on shafts. Essentially, drilling and turning bring these entities to life.
In the context of additive manufacturing, a designer doesn’t need to think about manufacturing tools or billets but about the limitations of the additive processes. Horizontal circular holes represent a good example of challenging shapes because of the overhang. Circular profile should be replaced with triangle, polygon or drop profiles.
In today’s AM literature, despite the growing amount of knowledge on the technological challenges and process comparison, there is a lack of methods allowing designers to effectively deal with the new possibilities. No comprehensive collection of design rules for DMLS or any standardized approach exists yet. Therefore, only manufacturing engineers experienced in AM processes from “trial and error” can best leverage their potential.
The lack of capable tools allowing a seamless incorporation of AM design rules is a serious impediment for a wider and cost-effective adoption of additive manufacturing.
Unique capabilities & constraints require a unique design framework
Materials sciences, computer-aided design (CAD) and engineering (CAE, through numerical simulation and optimization) have embodied separated domains and related software support. This contrasts with design engineering, which requires a more holistic approach to innovate and conceptualize new products.
Parts for additive manufacturing are usually designed in a solid modeling environment while they are oriented and attributed a support structure in another. As a result, independent designers are stuck with a disjointed process that requires costly iterations and communication with the manufacturing service bureau.
Building parts from a single material is another aspect of the classic paradigm. It is about to evolve because some additive manufacturing techniques can elaborate graded materials, offering gradients of physical properties and complex mechanical behaviors.
Moreover, by making lattice cellular structures feasible, additive manufacturing prompts designers to look beyond mere solids and flat surfaces. Unfortunately, tools that help generate such structures are hard to find in the current design software packages.
Designers’ interest in developing AM products that outperform current ones is real, but will require they modify the way they work (and think) when additive manufacturing is involved. Moreover, a grip on new advanced software will be required.
What Challenges Does Face a Designer When Using Additive Manufacturing?
Design for Additive Manufacturing (DFAM) is an emerging branch of mechanical design. Because it calls some changes in the way things must be done, along with it, appears a certain degree of resistance, from the early stages of the conceptual design to its virtual embodiment.
The first challenge for the designer is to avoid locking on current designs or traditional practices of DFMA. Another is to virtually create complex shapes either manually, by the means of tools for freeform modeling and reverse engineering or with material distribution algorithms. It takes a certain expertise on advanced softwares.
Taking into consideration the capabilities (and constraints) of AM requires a deep understanding of AM processes and of their design implications. It also requires a design environment relevant for DFAM:
- synthesizing the shapes, sizes, geometric mesostructures, material compositions and microstructures in order to leverage additive processes capabilities and achieve desired product performance
- supporting the modeling of specifications and parts, as well as the process planning and manufacturing simulations
Design for Additive Manufacturing Links Meso-scale Design to component (macro-)behavior
New capabilities offered by AM encourage the adoption of compliant “meso-scale” mechanisms or lattice cellular structures to achieve complex mechanical behavior. Tailored mesostructures are the geometric arrangement of materials on a scale that is insignificant when compared to a product component in which they are used.
For instance, it is possible to ally rigid materials with complex shapes to achieve heterogeneous material properties, and consequently target flexibility, in a product component. Cellular structures have also demonstrated certain benefits in thermal applications and biomedical applications.
A good approach to DFAM for linking geometrical structures to material properties is embodied through the general process-structure-property-behavior (or three-link chain) mapping model which originally links material science to material engineering.
This three-link chain model offers a resonant bond between the deductive cause-and-effect logic of science and the inductive goal-means relations of engineering.
Typically, mechanical designers choose from a toolbox of materials that have already been developed by material scientists. With DFAM, heterogeneous solid modeling denotes that material and other property information will be modeled along with geometry. Libraries of materials and mesostructures have yet to be developed to enable rapid construction of design models.
Ultimately, it will be possible to use performance-tailored mesostructures which can change or adapt the performance according to the given design requirements. The designer will have much more flexibility and capability to design a component with better functions.
In the Long Run, Generative Design Will Empower Additive Manufacturing
Today, a few CAD companies present their softwares as seamless design environments for additive manufacturing while others push prototypes of generative design platforms to the market.
Generative design brings the promises of interactive environments for parametric shape rule definition and design exploration in a guided movement through a space of possibilities.
Generative design is a powerful concept that automates different types of optimization - topology, lattice-based structures, and strut/beam structures. Relying on the infinite computing power of the cloud, it generates design alternatives to meet the exact specifications, based on a set of input parameters (desired weight requirements, maximum stress/strain) defined by a designer.
Generative design seems to marry engineering with the nature’s penchant for organic shapes and the optimization of geometries associated with living entities. This nascent approach and technology is a shift in the paradigm of designing things and a promising concept to improve the overall design quality, efficiency and performance. It is vowed to assist engineers in the additive manufacturing of lightweight and load-bearing components for the automotive, aerospace, industrial equipment and medical implant industries.
Although CAD solutions are becoming smarter, even an all mighty generative design algorithm still requires skillful engineers to enter the relevant specifications as inputs.
Spartacus3D offers engineering, consulting, and metal additive manufacturing services. The company seeks and applies the best practices for design engineering in order to unleash the potential of additive manufacturing and guarantee unrivalled satisfaction of its customers.