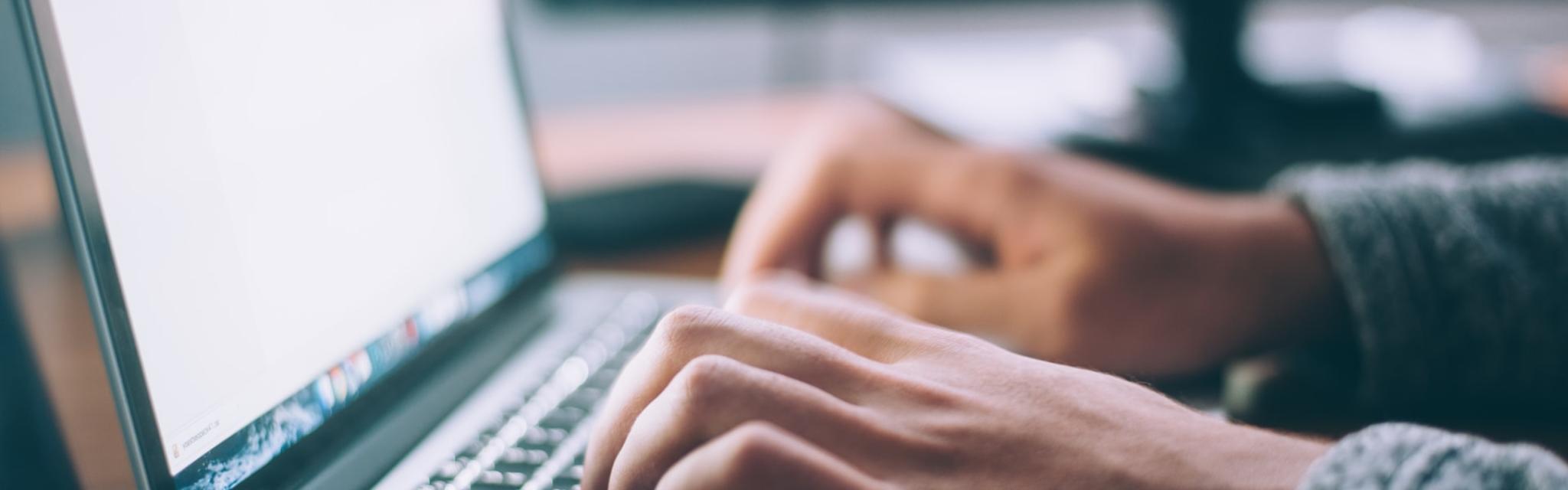
Excavators are massive off-highway machines, used to dig mainly trenches, holes and foundations. They are heavy-construction equipment that should be operated carefully. Excavators' heavy-duty design requires counterbalancing the weight of the excavated earth with a heavy counterweight. During the design phase of an excavator counterweight, possible dangers should be anticipated to guarantee the safe performance of the entire machine.
Counterweight related accidents happen mostly while operating the excavator or while removing a counterweight from it.
While transporting the excavated earth and turning the arm with the bucket to the right or to the left side or while lowering the load, the excavator counterweight, attached on its back, may swing. This tail-swinging effect can cause some dramatic accidents where bystanders get crushed between the tail-swinging counterweight and nearby walls or posts.
A counterweight is removed from the excavator to ease transportation. Because the counterweight is attached to the excavator in vertical position, danger of workers being struck by a falling counterweight is always potential in this procedure.
Improvements on the excavator counterweight should be implemented better yet during designing it to minimize the risk of safety issues.
The Best Improvements on Excavator Counterweight for a Safer Design:
1. Zero Tail Swing Design
Cast iron counterweights are heavy, but small, which allows them to remain inside the track width while swinging. This makes body swing safer and increases maneuverability in confined spaces. Still, zero tail swing excavators make work on slopes tricky by increasing the risk of tipping over. These designs are also more often applied to mini-excavators compared to heavier excavator variants.
2. Rear-view Camera
An integrated counterweight-mounted rear-view camera for the tail-swinging designs eliminates the need for the operator to turn and look at the back in order to ensure if there are no risk exposed bystanders when the crane swings. Otherwise the operator must be always extremely careful and makes sure no one gets caught by the tail swing.
3. Counterweight Removal System
Planning a counterweight hydraulic removal system during the design phase will help to detach a counterweight from the excavator easily and safely. It also reduces significantly the excavator's transport preparation time. FMGC recommends the usage of counterweights with built-in removal system only in particular cases, since they have smaller weight capacity than the standard ones.
In order to minimize the possible dangers the following safety and risk reduction guidelines should be followed on a regular basis.
Regular quality check of the excavator attachment and removal system
The whole removal hydraulic system and the lift chains should be regularly controlled in order to avoid any structural damage (included bending of the excavator frame or the lift mechanism; cracking of paint over joints, and spaces between the counterweight lift mechanism mounting brackets and excavator frame).
Labeling of the control functions of the counterweight removal system
The entire system for removal and attachment of the counterweight has controls in a side compartment of the excavator. All these dedicated valves and switches should be labeled to ease the work of the person, operating the attachment and removal system and avoid any wrong action.
Following the exact manufacturer’s instructions
All involved workers, no matter if excavators' operators or risk exposed bystanders should receive regular task training regarding the procedures to be followed in the safety aspects of attaching and removing the counterweight. Also all manufacturers’ instructions should be strictly followed.
FMGC works closely with the customer in order to choose the most suitable to his needs excavator counterweight design implementation. Experienced engineers take reliable decisions tailored to specific requirements. We provide a big variety of excavator counterweights, fully machined, with different weight (up to 20 tons), size, and shape, always adjusted to the excavator's assigned function.