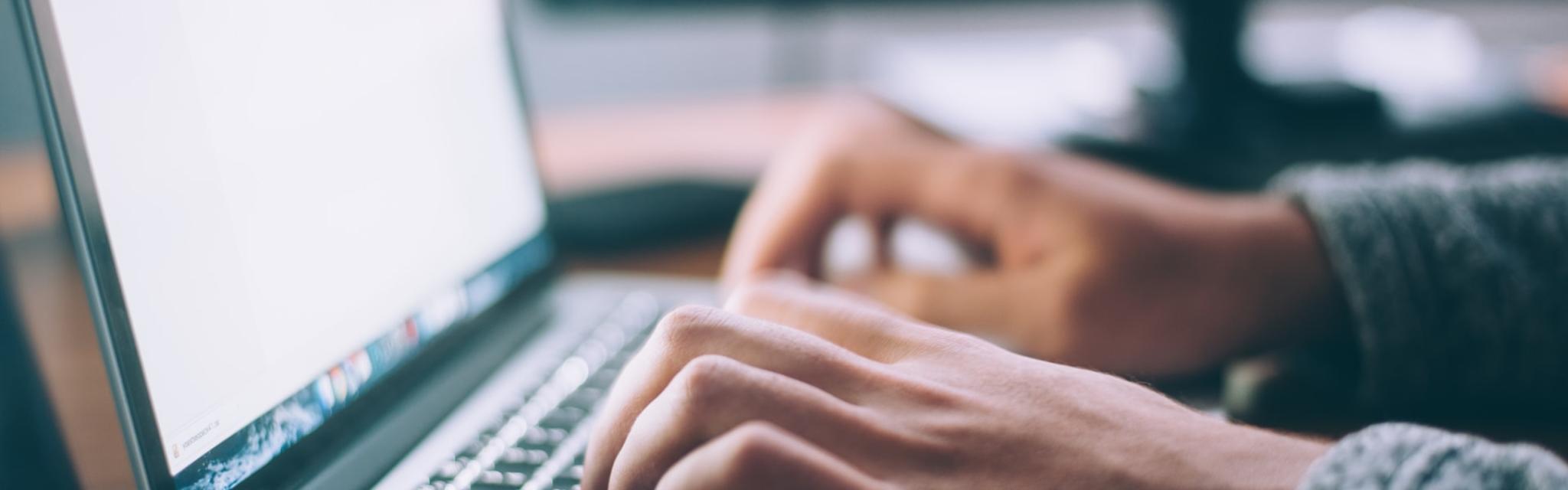
Titanium Ti6Al4V is the workhorse alloy of the titanium industry, also known as Grade 5, TA6V or Ti64. This α-β titanium-based alloy is the most commonly used of all titanium alloys and accounts for 50% of total titanium usage in the world.
Phase stabilizers are Aluminium and Vanadium. Al reduces density, stabilizes and strengthens α while vanadium provides a greater amount of the more ductile β phase for hot-working.
The detailed composition of the alloy is described below:
Chemical composition of titanium Ti6Al4V (TA6V, Ti64).
Ti6Al4V exhibits strength-toughness combinations between those of steel and aluminum alloys, has the same stiffness than commercially pure titanium but is significantly stronger.
Mechanical properties of Ti6Al4V compared with other metals
Additionally, this alloy can be heat treated for several purposes:
- Reduce residual stresses developed during fabrication (stress relieving)
- Produce an optimum combination of ductility, machinability, or dimensional and structural stability (annealing)
- Increase strength (solution treating and aging)
-
Optimize special properties such as fracture toughness, fatigue strength, and high-temperature creep strength.
A suitable grade for stringent aerospace requirements
Typical applications can be fracture-critical parts, low and high temperature components and structures (such as airframe, fasteners, discs, hubs, spacer, seals, compressor blades, structural parts and complex turbine engine components).
Ti6Al4V components can make up a third of the dry weight in a jet engine.
Additive Layer Manufacturing (ALM): An opportunity to ease titanium parts production
-
From the fabrication
Just as it is in forging of titanium α-β alloys, it is essential to consider during its machining (or welding) the effect of energy input (heat, deformation) on the microstructure and material properties. Despite a good formability (ability to undergo plastic deformation without damage), the low thermal conductivity and high mechanical properties of Ti6Al4V complicate traditional subtractive machining, compared to stainless steels.
Indeed, the deformation mechanism during Ti6Al4V machining is complex and causes basic challenges, correlated and affected by each other, such as high stress on cutting tool, high temperature, high tool wear, saw tooth chips and undercut parts. If a substantial volume of material is to be machined away, it becomes expensive and time-consuming because of the proper conditions to apply: low cutting speed and feed rate, large quantities of cutting fluid, sharp tools and a rigid setup.
In the form of metal powder for ALM, Ti6Al4V is expensive too, but one can achieve far less waste in the process (smaller buy-to-fly ratio). Last but not least, the compressive residual stresses created from machining and advantageous for fatigue resistance can also be obtained by shot-peening at the end of the ALM value chain.
-
Through the welding…
Ti6Al4V elements are routinely joined by several fusion welding techniques, (gas-metal or plasma arc, electron or laser beam), or by brazing or solid state joining techniques (diffusion or inertia bonding, friction welding).
The very essence of joining Ti6Al4V or CP Ti is to exclude detrimental interstitial elements, contaminants (scale, oil, etc.) from the joint region and to avoid prejudicial phase changes in order to maintain the joint ductility. Welding environment, cooling speed and hydrogen content may favor brittleness, but welds in Ti6Al4V are relatively high in fracture toughness, due to the transformed products they contain. In Aerospace industry, a stress relief operation is generally applied after welding to minimize residual tensile stresses in welds that are used in fatigue critical applications.
Basically, welding operations of highly functional Ti6Al4V parts are complex, expensive, time consuming and must be performed rigorously to be successful. Aerospace can a take a real advantage of additive manufacturing in the ability to consolidate design by reducing the number of subcomponents and the need for joining, brazing, welding and assembling in general.
-
To the heat treatment…
In titanium α-β components, microstructural configuration is not only controlled by how much deformation occurs during processing or how high the temperature is when the alloy is processed, but also by the section thickness of the component.
Ideally, alloys should have a good quenchability (to reach in fairly thick sections, the desired cooling rates and microstructural hardness). However, many α-β alloys don’t. Ti6Al4V can barely be effectively hardened in sections less than 25 mm thick. Thicker sections can be heat treated, but center regions will not achieve desired microstructure and will thus fail to reach optimum property levels.
Since the optimum hardened properties are obtained in small cross sections that are rapidly quenched, it is recommended to design parts with sections as thin as possible when heat treatment of structural strengthening is foreseen. ALM encourages more freedom than traditional manufacturing methods and, in some extent, allows the fabrication of parts with free-form, intricate, topologically optimized or complex geometries that comply better with heat treatment requirements.
Additive Layer Manufacturing (ALM) Is An evolution of investment casting: Higher Design freedom & better material properties
Casting has offered several benefits, among which, one is directly parallel with its ALM counterpart: the ability to produce very complex shapes easily. By discarding investment casting in favor of ALM, better mechanical properties can be realized without sacrificing the ability to design complex and freeform shapes.
The unique ALM metallurgy allows metal ALM processes to produce parts with material properties similar or superior to their traditionally manufactured counterparts. Typically, Ti6Al4V components produced by investment casting have inferior properties than those from wrought material.
While Titanium has been used from more than 50 years in Aerospace industry, the additive manufacture of Ti6Al4V components can bring further improvements to current aerospace applications, as well as encouraging new ones.
Spartacus3D has recognized the potential of printed titanium components in terms of performance (designs allowing more effective heat treatments, reduction of failure risks with fewer welds), with less material wastes and better lead times.