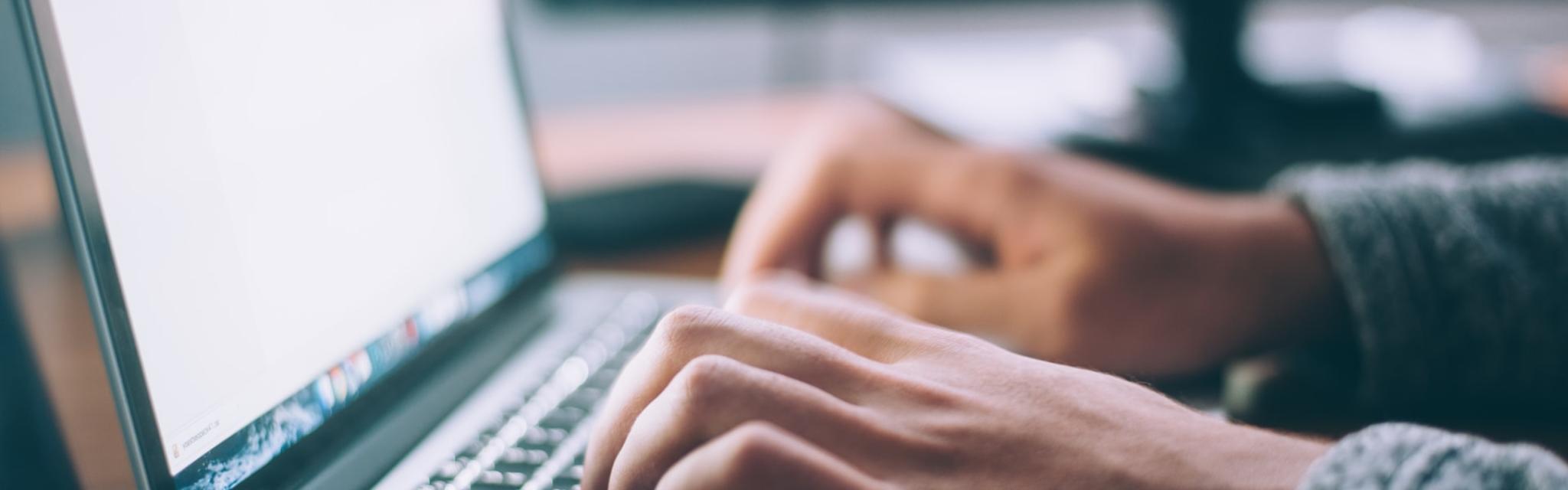
FMGC Protecting and Ballasting Shells Support the Highest Performance of Your Oil and Gas Platform
The oil and gas industry is one of the “motors” of today’s industrialization. To ensure future supplies, the sector is continuously investing in innovations. One of them is the positioning of oil rigs into deeper waters. This move would require some additional adjustments of currents structures and the design, manufacture and supply of new ones.
Subsea cables have always played and now even more than before a substantial role in oil and gas projects. Submarine cables protection is of critical importance to the successful outcome of the entire installation.
What Are the Functions of Submarine Cables Deployed at an Oil and Gas Platform?
To better understand why submarine cables protection is of highest priority, it is first important to realize the important functions of subsea cables. Here are some of them:
- connecting oil and gas platforms to mainland power grids
- transmitting data and internet traffic
- providing high-quality and reliable shore-to-platform and internal platform fiber-optic communications
- providing oceanographic monitoring and surveillance
In general energy and telecom submarine cables are deployed in almost any single step of an offshore project from exploration and production through storage and transport. Exposed to tough conditions as heat, cold and saltwater, their protection is crucial to their performance. Furthermore, oil rigs installed in deep waters require much longer cables and respectively a mechanism that can protect the cable along its length.
The Challenges of the Sector
The installation of oil and gas subsea cables is a laborious process. The crew often has to work under extreme weather conditions and technicians have to regularly check if all systems – above and under water are working properly. Oil and gas installation are subject to ocean current strength and strong loads.
What is an Oil and Gas Project Expecting from the Performance of the Subsea Cables?
The biggest requirement from oil and gas project managers to subsea cables manufacturers is reliability. The sector expects to be provided with a wide range of cables for energy, control and data, featuring high-quality and low maintenance needs. One of the first things to mention when ensuring the reliability of the submarine cables is their protection.
How Do FMGC Protecting and Ballasting Shells for Submarine Cables Can Solve the Problems of the Oil and Gas Industry?
The constantly increasing complexity of the new floating vessels engineered and deployed to operate in deep waters are more and more dependent on fast, reliable and secure broadband communication transmitted by submarine cables. Damages to subsea cables are not common, but when they happen, this might have catastrophic impact. Ruptures are usually caused by fishing, vessel anchoring, gas extraction or the installation and maintenance of renewable energy projects. Submarine cables can get also damaged by hurricanes or earthquakes. Timely repairs are expensive , critical and therefore the protection mechanism should be easy and fast to maintain.
FMGC cast iron shells are the final product of the collaborative and innovative R&D project IBOCS and are especially designed to fulfill the specific requirements of the offshore sector. The aim of the project was to develop a full range of articulated cast iron shells that protect, ballast and stabilise subsea conducts (cables, pipes, etc).
Made of gray cast iron, the main goal of the FMGC protecting and ballasting shells is to significantly reduce the cost of the electrical connection for MRE solutions and thus - the cost of the kWh.
FMGC has developed a wide range of shells that can adapt to different types of cables: from telecom cable of 20mm to export cable of 300mm. We can easily adapt the required kilograms for each cable segment (from 30kg/m to 250kg/m), depending on the specific seabed conditions, since all FMGC shells have the same joint system. Therefore for the same diameter of cable, we can easily alternate the type of shells along the cable route.
FMGC cast iron shells with integrated ballast provide most reliable and robust protection. The protecting and ballasting shells are especially designed to resist high impact, abrasion and corrosion. The unique mechanical properties of cast iron withstand the harshness of marine environments. Every shell comes with integrated ballast and bendrestrictor functions, which eliminates the risk for overbending or dislocation during the installation and maintenance operations.
FMGC can calculate and analyze the required ballast weight for the cable based on metocean and soil data. Our partner INNOSEA can conduct, if necessary, some additional studies to ensure the weight needed to stabilize the cable and identify potential weight and cost savings.
The cast iron protecting and ballasting shells for submarine cables offer:
- Sufficient weight and thickness to stabilize and protect the cables
- A hydrodynamic design
- An increase in the bendradius to match that of the cable and the undersea relief
- A transfer of tensile forces during the installation of the cable
- Sufficient mass for the entire duration of the immersion period (20 years minimum)
- A simple, robust and economical design
Consult here the technical specifications of FMGC protecting and ballasting shells.
Just a couple of years ago, working on an offshore oil and gas platform used to mean isolation from the mainland for months. Most recent developments in submarine cables made communications simple and instantaneous. A reliable subsea cables protection is an essential part of a successful offshore oil and gas project. FMGC offers the sector an innovative solution, designed and manufactured especially to meet the challenges of the industry. The FMGC protecting and ballasting shells made of cast iron ensure cable’s protection, stability, strength and best possible performance.