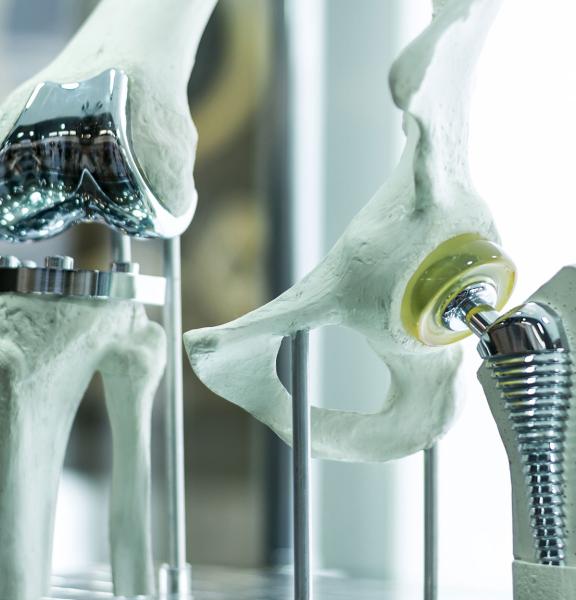
Farinia Group is always looking for new ways to diversify its industrial operations. Relying on our subsidiaries' century-long expertise in material transformation, our engineering teams continuously transfer their know-how to new, high-value and challenging applications.
Medical devices companies across the world today are more focused than ever on developing innovative products for global orthopedic demand. This demand is driven by surgeons and caregivers to provide better clinical outcomes to patients and reducing hospital stay.
In particular, the market of metallic devices (implants, prostheses) is doomed to a high growth for the years ahead. Examples of promising applications are surgical instruments and medical implants.
The manufacturing of medical implants (artificial joint prosthesis, trauma implants and spinal implants) represents a great opportunity for the Group. The production of high-end medical implants will inevitably shift from conventional techniques to additive manufacturing to benefit unique design capabilities and supply-chain advantages.
Incorporation of trabecular structures accelerate osseointegration and enhance implant-body compatibility. Cellular lattices geometries mimic bone mechanic characteristics to reduce stress-shielding and bone resorption. Custom and patient-specific interfaces ease implant insertion, improve comfort and speed up healing and restoration of patient’s mobility.
Spartacus3D, Farinia Group's subsidiary specialized in metal additive manufacturing, aims at leveraging this powerful technology to produce highly functional and tightly adjusted metal implants.
We have put huge efforts to master the additive manufacturing's value chain from the powder qualification to the part post-processing and inspection. Significant investments were also achieved to integrate in-process monitoring and dedicate a machine to medical-grade titanium.
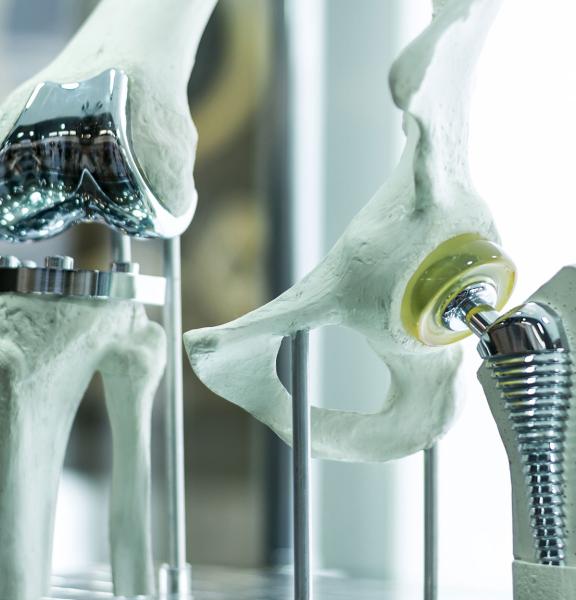