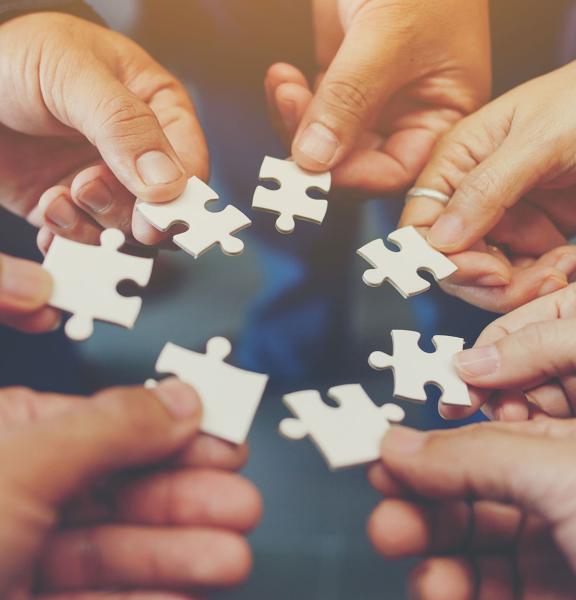
Forging hammers are used in the drop forging to form the metal between two dies. The first half of the die is attached to the anvil and the second part to the hammer. The material is placed in the lower die and then hammered with the upper one until the hot metal flows in all directions, filling the die cavity. Drop forging is the first industrial process which had been developed for closed die forging, before the introduction of presses.
Hammers use impact strain to deform the material. The ram is thrusted into the workpiece with a speed of more than 1/1,5 m/sec by sequence of several continuous blows on the same die; on the contrary - forging presses need only 1 to 2 strokes. Hammers are characterised by the energy produced in each blow (stroke), which is indicated in J, kJ and kg-m. A hammer of 250 kJ (25 000 kgm) produces on each blow an energy equivalent of the drop of a mass of 25 metric tons from 1 m height.
Hammers are classified in single effect (drop forging), double effect and counterblow hammers, depending on the drive of the ram movement. These are very flexible and polyvalent tools, and therefore dedicated mostly to small and medium series production. However, automatic hammers have been developed to produce automotive parts in big series such as connecting rods for automotive and trucks engines. Hammers are particularly suited to the forging of thin components (such as con rods, airfoils) and heavy parts, made of steel, Ni-based alloys or titanium.
Setforge owns excellent machinery and tooling equipped with best dies. We use single, double effect and counterblow hammers, for all business fields, for steel, stainless steel, Ni-based alloys and titanium components.
Companies specifications expand_more
Setforge La Clayette
Located in the south of Burgundy, Setforge La Clayette was founded almost 100 years ago, and has a long tradition of metalworking. Our components are made of steel, stainless steel, aluminum, titanium, Inconel and other superalloys.
Setforge Estamfor
Setforge Estamfor specializes in hot forging, machinery and assembly. Through our established network of reliable subcontractors, we also supply finished coated parts. Our quality components are highly appreciated by the French and international manufacturing markets.
Setforge L'Horme
Since 1906, Setforge L'Horme, a subsidiary of Setforge, has provided complete manufacturing services including forging, machining, painting, heat treatment and assembly.