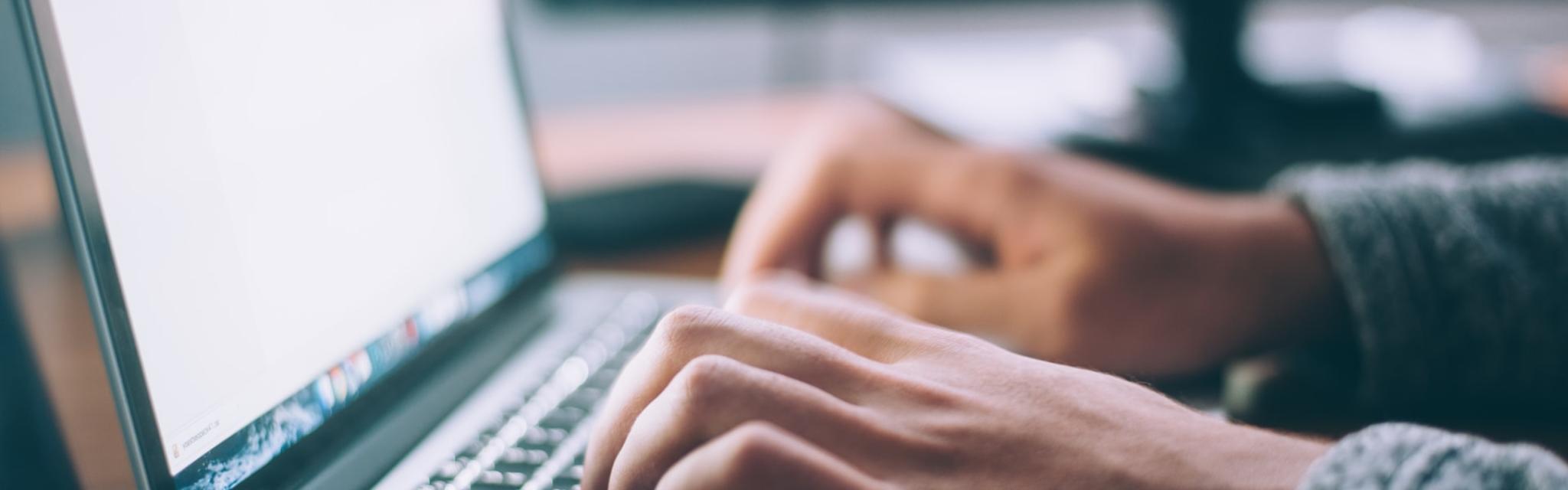
The importance of submarine power cables has increased steadily with the tremendous development of the telecommunications, oil and gas and marine renewable energy industries. Their main function consists in carrying electric power below the surface of the water. Some of their main applications are connecting offshore oil production facilities, establishing interconnections between networks, supplying electricity to remote areas and many others.
In the Marine Renewable Energy sector submarine cables are used to connect the different wind turbines in a wind farm. Higher capacity submarine cables are then required to export the power from a wind, wave or tidal installation to an onshore grid connection. Thus, the generated power is fully dependent on the quality of the submarine cables. And although submarine cables are designed to be strong and resistant, faults occur and can temporarily affect supply.
Therefore submarine power cables are considered in Europe as critical infrastructure and special attention is paid to their installation, protection and maintenance.
What Are the Main Challenges Facing the Submarine Power Cables Sector?
Submarine power cables are subject to damage when not properly installed and not properly protected.
Many existing offshore wind farms have to deal with cable problems, most frequently during the installation stage. The critical point is that damages caused by improper installation can become obvious immediately or many years later. The repair of a submarine power cable may vary from weeks to many months, depending on the vessel and the cable’s damage. The cable is brought to the surface and a piece of stock cable is inserted into the original cable to connect the two ends. This is a laborious and expensive process.
In terms of submarine cables protection, they are several common methods, including direct burial, concrete mattresses and rock trenching. Depending on the project and the length of the cable, one of them is applied. However, all existing conventional methods show some disadvantages at certain point, usually in terms of corrosion, cost-efficiency, bending radius, design or fatigue of the electrical conductors.
The fast development of the marine renewable energy sector and the customer demand for increased power requirements and improved reliability put the spotlight on the quality of submarine power cables and expect better performance.
The Right Answer Comes From IBOCS
In 2014, FMGC has launched a collaborative and innovative R&D project in partnership with Innosea (engineering company) and Gem (laboratory of Nantes University and Centrale Nantes) to answer the specific expectations of the Marine Renewable Energy industry. The aim of the project was to develop a full range of articulated cast iron shells that protect, ballast and stabilise subsea conducts (cables, pipes, etc) and a semi-automatic installation equipment.
The goal of this solution is to reduce significantly the cost of the electrical connection for MRE solutions and through it, to reduce the cost of the kWh. FMGC protecting and ballasting shells are also suitable for Oil&Gas, Telecom and International Electrical Connection applications.
FMGC Protecting and Ballasting Shells
Installation of FMGC Shells for Sabella
After several months of intense collaboration, the IBOCS consortium designed, manufactured and tested its first shells in February 2015. 40 m of cast iron shells (réf : IBS-70-88) around a 69 mm in diameter electrical cable have been installed near Ushant in the Fromveur, one of the most powerful stream of Europe. Subject to the specific site conditions and the very bad weather (strong storms and tides) the cast iron shells have fully ensured the stability and protection of the electrical cable.
FMGC have then supplied 200m of shells to protect the cable of the tidal turbine Sabella D10, which have been successfully installed in June 2015.
➤ WATCH THE INSTALLATION OF THE SABELLA D10 SUBMARINE CABLE, EQUIPPED WITH FMGC BALLASTING SHELLS
This solution aims at eliminating all known challenges concerning the protection and installation of submarine power cables today.
Advantages of FMGC Protecting and Ballasting Shells
- Sufficient weight to maintain the stabilization of the cable on the ground without resorting to external elements as concrete mattress or rock-dumping.
- An innovative design for increased stability of the cable and reduced fatigue of electrical conductors.
- A design which increases the bending radius in order to make it closer to the bending radius of the cable to fuse with the relief of the seabed and thus improves the stability and the fatigue of the cable.
- During installation the cable is subjected to tension. The design of the FMGC solution allows the transfer of this tension to the shells and thus protects the cable.
- FMGC protecting and ballasting shells possess sufficient quantity of cast iron to ensure the proper function of the ballast for 20 years, taking into account corrosion levels.
- A simple and strong design to minimize the price for supply of the envelope and its installation.
Advantages of the Semi-Automatic Laying Device
- Increase in the installation’s speed to get as closely as possible to the installation’s speed of the single cable.
- Decrease the hardness of the operating method.
- Decrease the cost of the cable installation by proposing a way of semi-automatic laying device.
- Increase the safety and the working conditions for this operation.
➤ DISCOVER MORE FROM FMGC ON SUBMARINE CABLE PROTECTION
FMGC has developed in collaboration with IBOCS a wide range of shells suitable for different types of cables: from telecom cable of 20mm to export cable of 300mm. Since all shells possess the same joint system, the needed kilograms for each cable segment (from 30kg/m to 250kg/m) can be easily adapted, depending on the specific seabed conditions. Thus, for the same diameter of cable, the type of shells along the cable route can alternate.
FMGC can calculate and analyse, in partnership with INNOSEA, the required ballast weight for the cable based on metocean and soil data. If necessary, we would recommend some additional studies to ensure that the estimated weight is sufficient to stabilize the cable or identify potential saving weight and cost.