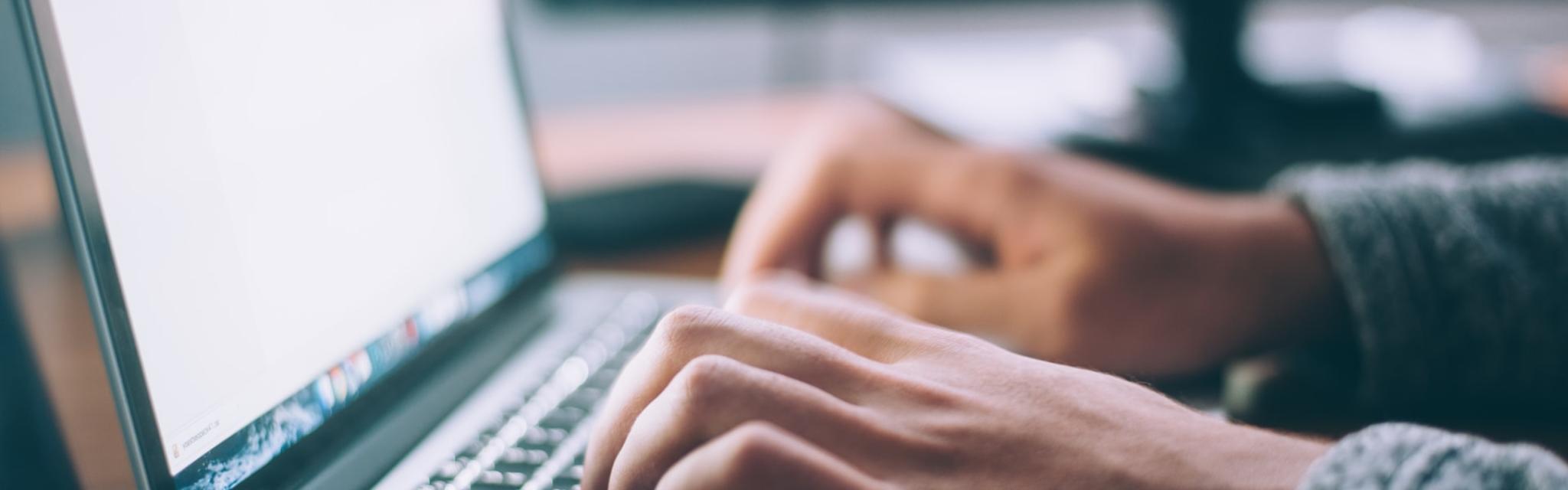
Tidal turbines are placed underwater to produce electricity by capturing the hydrokinetic energy of consistent, fast-moving currents. Tidal energy is recognized as the electricity generation of the future because of its contribution to a better world with less carbon dioxide. Ebbs and flows are natural tides movement; therefore the output of a tidal current electricity generation system is predictable. This makes it much more interesting to investors than the wind, wave and solar devices.
Tidal turbines present a unique configuration of sophisticated components. Every turbine consists of a big windmill with blades and foundation. The foundation plays an integral role since it secures the stability of the entire system. Currently the most common once are using drilled piles or the so called monopoles. Although very robust, compared to gravity foundations this technique is extremely expensive in terms of:
- seabed geology and bathymetry analysis,
- complicated design,
- additional machinery for installation and
- often required maintenance.
The French company SABELLA has developed a new tidal turbine with a revolutionary gravity based foundation that delivers best results and requires less cost for maintenance and installation. The SABELLA tidal turbine is fixed to the seabed with cast iron ballast; without any penetration. The high density ballast should fulfill certain requirements in order to secure the perfect performance of the tidal turbine base. Although it can be made of concrete, FMGC strongly recommends the use of gray cast iron because of the following reasons:
Density and Product Cost
Metal is proven denser than concrete, which enables laminar iron to achieve the target weight in less space and volume compared to concrete. Concrete's density can be improved through additional aggregates as limonite, hematite, or magnetite or a mixture of metal scarps and bits, which increase the cost, but doesn't make the concrete denser than the metal.
Resistance
Once the foundation has been designed the counterweights should be attached to it with screws or another fastening technique. Since cast metals are stronger and harder than concrete, gray cast iron counterweights are much more resistant to impact and strains. The biggest challenge for the tidal turbine base comes after it has been placed on the seabed. On the one hand the high density ballast should secure stability against the strongest current tides but it should also carry the entire construction. The engineers count on the resistant mechanical properties of cast metal when installing the configuration.
Corrosion protection
The biggest problem of every marine technology device is its resistance level to corrosion.
Tidal turbine ballast made of gray cast iron need only paint and coating to stay protected. As opposed to this concrete counterweights need additional containers to keep them from any environmental impact, which significantly affects the cost, but doesn't deliver better protection.
FMGC manufactures tidal turbine high density ballast counterweights made of gray cast iron that can vary in weight up to 20 tons. We support the vision of SABELLA for better marine technologies and therefore always provide innovative solutions. Our mission is to harness tidal energy in a best way in order to deliver clean energy future.