HEAT TREATMENT
Setforge has numerous in-house heat treatment possibilities. Discover our possibilities!
KEY PROCESSES
Heat treatment is a fundamental operation in the production process of a mechanical part. By acting on the microstructure of steels and alloys, it makes it possible to obtain the mechanical characteristics required for the use of the component. For example, by increasing the surface hardness, ductility or impact resistance.
In practice, heat treatment alternates predetermined cycles of heating, holding and cooling. Among the most common heat treatment operations are: annealing, quenching and tempering and thermochemical treatments.
Setforge experts are able to assist you in choosing the best heat treatment for your application. Depending on your needs, heat treatment operations are carried out in-house by our companies or via one of the group's partners of excellence.
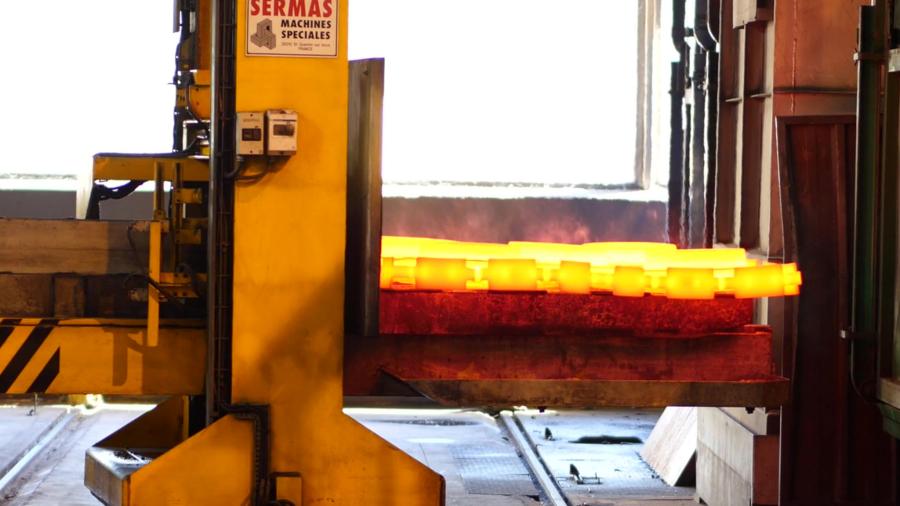
NADCAP HEAT TREATMENT certification
OVERVIEW OF HEAT TREATMENT TECHNIQUES
There is a multitude of heat treatments adapted to the steels used and the desired mechanical characteristics. It is also possible to combine several treatments to obtain the desired result. As this is a very complex discipline, we propose here to give you a brief overview of the main categories of heat treatment.
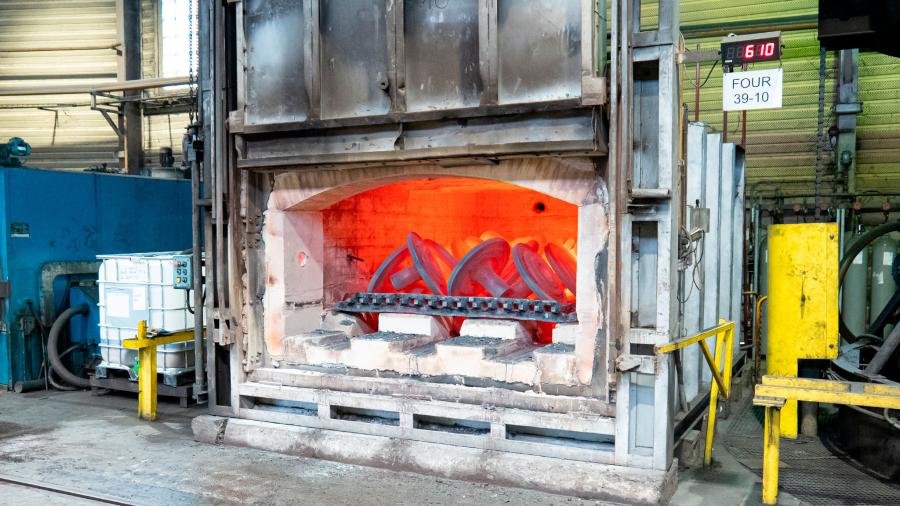
ANNEALING
These types of heat treatment restore the original properties of the material that was modified during the production process. The plastic deformations that take place during forging will introduce internal stresses to the materials and reduce the ductility of the part, making the subsequent operations more complex.
In practice, annealing involves heating and holding followed by slow cooling. There are various types of annealing, such as softening, stress relieving, homogenizing, etc.
Goal and advantages
- Causes the formation of structures favourable to machining
- Eliminates or reduces internal stresses in the workpiece
- Eliminates the effects of plastic deformation on the structure
- Prepares the structure for further heat treatment
QUENCHING AND TEMPERING
This is a hardening process. It is carried out through three successive stages: austenitization, quenching and tempering.
The first step is to heat the steel and keep it in its austenitic range. During this stage the structure of the steel becomes homogenous. The second step is quenching, which consists of rapidly cooling the metal by immersing it in a water or oil bath. This step increases the mechanical characteristics of the metal and its hardness.
The last step is tempering. This is carried out directly after quenching and consists of heating at a low temperature for several hours to remove the internal stresses caused by rapid cooling.
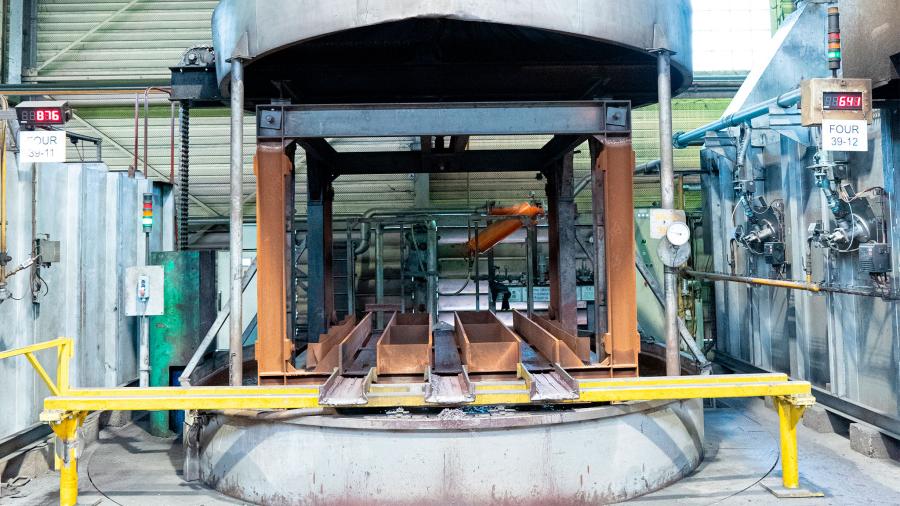
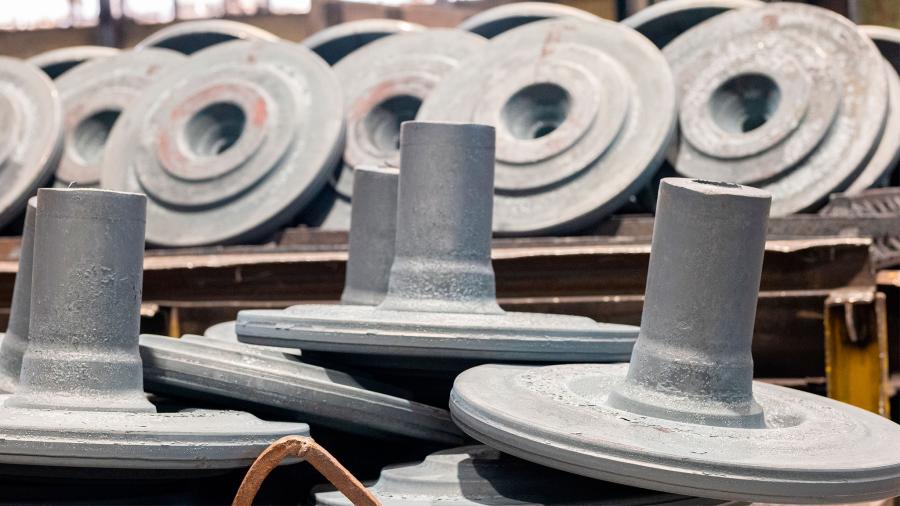
THERMOCHEMICAL TREATMENTS
Unlike previous treatments, thermochemical treatments act on the chemical composition of a certain thickness of the surface layer of a metal part in order to give it particular properties.
The most common treatments are :
CASE HARDENING - Allows the surface carbon content to be increased in order to increase the surface hardness of the steel part.
NITRURATION - Forms a nitrided layer that improves surface hardness. Performed at lower temperatures than case hardening, it is recommended for parts subject to wear, seizure and fatigue.
NITROCARBURING - A variation of the nitriding process, this process is carried out to achieve wear resistance of the surface layer and improve fatigue resistance. The low temperature of the process limits deformation and economic cost compared to case hardening.
CARBONITRATION - Provides a hard, wear-resistant case-hardened layer.
Would you like to know more about heat treatment ?
OUR TEAMS ARE AT YOUR DISPOSAL !